Building Insulation and Dry Lining Products Market Report – UK 2024-2028
Available as an Instant Download PDF
The latest edition of the UK Building Insulation and Dry Lining Products Market Report – 2024-2028 offers a thorough analysis of the UK market for insulation and dry lining products. It covers the market structure, major trends, and growth drivers while providing a detailed evaluation of key suppliers and the competitive landscape.
The report also assesses the impact of economic factors, such as rising energy costs and material price inflation, on market dynamics. Additionally, it reviews government initiatives, regulatory changes, and future growth prospects across both residential and non-residential construction sectors, emphasizing sustainability and energy efficiency.
£1,499.00 Exc. VAT
Impact of Economic Factors
The report analyses how rising energy and raw material costs, along with inflationary pressures, have influenced product pricing and overall market growth. It also considers the effects of the weakened pound on import costs and market value.
Government Policy and Regulation
A significant focus is on how government policies, such as updated Building Regulations (Part L) and the upcoming Future Homes Standard, are driving demand for insulation and energy-efficient building solutions. The report also explores the influence of the Great British Insulation Scheme on retrofitting.
Market Segmentation and Demand Shifts
The report examines demand patterns across residential and non-residential sectors, with particular attention to new builds versus retrofits. It highlights a shift away from government-subsidized retrofits and the growing importance of housebuilding and non-residential sectors.
Technological and Product Innovations
There is a discussion of advancements in insulation materials, particularly in products that meet high energy efficiency standards with a thinner profile, suitable for offsite construction methods and prefabricated building panels.
Competitive Landscape and Supplier Dynamics
The report provides insights into the market’s major players, including Kingspan, Knauf, Rockwool, and other suppliers. It discusses market shares, recent investments in production, and how competition is shaping product offerings.
Challenges in Retrofitting and Homeowner Reluctance
A key issue explored is the ongoing need for financial incentives to encourage homeowners to adopt insulation measures, especially for costly projects like solid wall insulation. The report highlights the potential for retrofitting millions of uninsulated dwellings, despite the low current uptake.
Future Market Growth Prospects
The report includes growth forecasts, outlining factors expected to drive the market value to £2.5 billion by 2028, and assesses the role of sustainable construction practices and increased insulation standards in shaping future demand.
Product Category
The following product categories are explored throughout the report.
Mineral Wool Insulation
This is the largest product category by market share, favoured for its thermal efficiency, fire resistance, and suitability for a range of applications, including walls, roofs, and floors. Mineral wool is widely used in both new builds and retrofits and is a popular choice in non-residential construction, particularly for flat roofs and metal cladding systems.
PUR/PIR (Polyurethane/Polyisocyanurate) Insulation
Known for high thermal performance, PUR/PIR products are often used in applications where thin profiles and high insulation values are needed, such as prefabricated panels for walls, roofs, and floors in new construction. These materials are especially suitable for offsite construction methods and are often chosen to maximize internal space.
EPS (Expanded Polystyrene) and XPS (Extruded Polystyrene) EPS and XPS
This insulation are popular choices for external wall insulation systems and cavity walls, offering good thermal performance at a relatively low cost. EPS, in particular, is used in both residential and commercial projects, whereas XPS, with its greater moisture resistance, is often selected for below-ground and foundation applications.
Rigid Board Insulation
Rigid insulation boards, made from materials like phenolic foam or cellular glass, are used where high structural stability and thermal resistance are required. These boards are particularly suited for non-residential applications and often installed on flat roofs, walls, and floors that require added durability and high insulation standards.
Reflective and Multi-Layer Insulation
These products include multi-layered foil-based insulation systems designed to reflect heat, providing thermal and vapor barriers. Commonly used in applications like roof spaces, they are often combined with other materials to enhance insulation performance in confined spaces where thicker materials are impractical.
Dry Lining Systems
These systems include plasterboard, wallboard, and other panel systems used primarily in internal wall linings. Dry lining offers quick installation and provides insulation as well as soundproofing, commonly applied in both residential and commercial interiors to create insulated, smooth wall surfaces.
Loose Fill and Blown Insulation
This category includes materials like cellulose, fiberglass, and mineral wool that are installed as loose fill or blown into spaces. They are primarily used in retrofit applications for lofts, cavity walls, and other areas where standard insulation panels are difficult to install.
The UK Building Insulation and Dry Lining Products Market Report – 2024-2028 provides a comprehensive overview of a market undergoing transformation, influenced by regulatory shifts, economic pressures, and increased focus on sustainability.
Following a period of decline during the COVID-19 pandemic, the market saw a strong recovery beginning in 2022, supported by government initiatives aimed at reducing carbon emissions and improving energy efficiency.
The introduction of updated Building Regulations, including Part L amendments, and the Future Homes Standard slated for 2025, have heightened demand for high-performance insulation products. This regulatory environment, coupled with economic factors such as rising energy prices and raw material costs, is reshaping market dynamics and prompting price adjustments across the industry.
Demand patterns are shifting significantly, with new housebuilding and non-residential construction now key growth drivers, as the domestic retrofit sector has declined due to reduced government funding. While traditional mineral wool remains the dominant insulation material, demand for alternative high-efficiency products is growing, particularly those suitable for prefabricated and offsite construction.
Additionally, insulation standards are increasingly stringent, driving innovation as manufacturers strive to meet efficiency requirements with thinner-profile materials that maximize internal space. Leading manufacturers, including Kingspan and Knauf, are investing in production capacity and product innovation, signaling confidence in the long-term growth of the insulation sector.
Forecasts for the UK insulation market indicate steady growth through 2028, with an expected annual increase of approximately 6% and a projected market value of £2.5 billion.
Continued adoption of energy-efficient building solutions and advancements in technology will fuel this growth, though challenges remain, especially in the domestic retrofit market were cost barriers limit homeowner uptake.
There is a substantial market potential for retrofitting uninsulated housing stock, particularly solid walls and lofts, though financial incentives may be necessary to boost adoption rates.
The report underscores that while economic and regulatory factors will continue to shape market performance, the drive for sustainable construction and energy efficiency will be critical in supporting long-term demand.
Government Policies and Regulatory Changes
Significant updates to Building Regulations, particularly Part L, and the forthcoming Future Homes Standard are central to the market. These regulations mandate higher energy efficiency and lower carbon emissions for both residential and non-residential buildings, directly increasing demand for insulation products. Initiatives like the Great British Insulation Scheme also aim to drive retrofitting efforts across the UK’s existing housing stock.
Sustainability and Carbon Reduction Commitments
The UK’s commitment to meeting carbon reduction targets and improving building performance has created a strong demand for energy-efficient insulation. The construction industry’s focus on sustainability is driving growth in the market for high-performance insulation materials that meet or exceed efficiency standards.
Rising Energy Prices and Inflation
Increased costs for energy, especially after the Russia-Ukraine conflict, along with inflation in raw materials, have influenced insulation pricing and overall market growth. Higher energy costs are also encouraging consumers to invest in insulation as a means to lower utility bills, particularly in the domestic sector where cost-effective insulation options are attractive.
Technological Advancements in Insulation Materials
The push for thinner, high-performance insulation materials is reshaping product offerings, especially for use in prefabricated and offsite construction, where maximizing usable space is essential. Advances in mineral wool and PUR/PIR products, which offer enhanced energy efficiency, are responding to the need for sustainable building practices.
New Build and Non-Residential Construction Growth
Increasing levels of housebuilding to meet government targets and the sustained growth in the non-residential sector, particularly in flat roofs and cladding systems, are key drivers. These segments now represent substantial portions of the market as government-funded domestic retrofits have declined.
Financial Incentives and Retrofits
While there is massive potential for retrofitting the UK’s existing uninsulated housing stock, adoption rates remain hindered by high costs, especially for solid wall insulation. financial incentives or subsidy programs are needed to encourage homeowners to invest in retrofitting for better energy efficiency.
Competitive Landscape and Supplier Strategies
Major players like Kingspan and Knauf are investing in production and product development, signalling confidence in the market’s long-term growth. Increased competition is also fostering innovation and specialization, with companies focusing on sustainable, cost-effective solutions to meet changing market demands.
Regional Construction Project Analysis
Demand varies across the regions due to factors like regional construction activity, housing stock characteristics, and local government policies on energy efficiency.
England
England represents the largest share of the insulation market due to its higher volume of new builds and extensive retrofitting needs, particularly in urban areas with older housing stock.
Demand is strong in both residential and non-residential sectors, driven by significant housebuilding activity in the Southeast and Southwest. Localized incentives and policies promoting energy-efficient construction and retrofitting also contribute to market growth in key urban centers like London and Manchester.
Scotland
In Scotland, demand is robust for both new build and retrofit insulation due to the government’s strong commitment to carbon reduction and energy efficiency. Scottish policies, such as energy efficiency standards for owner-occupied homes, are driving investment in insulation products, particularly in rural areas where heating costs are high. Scotland’s colder climate further supports the need for high-performance insulation to enhance energy efficiency and reduce household energy bills.
Wales
In Wales, demand is largely centered on retrofitting older, poorly insulated housing stock. The Welsh government’s initiatives, such as the Optimized Retrofit Program, aim to reduce carbon emissions from existing buildings, supporting a steady demand for cavity walls and loft insulation.
New construction is slower in Wales compared to other regions, but government-backed energy efficiency programs continue to drive demand for insulation products.
Northern Ireland
Northern Ireland’s market for insulation is smaller but growing, primarily driven by retrofitting needs and local incentives to improve energy efficiency. With a high percentage of older housing stock, there is significant potential for retrofitting projects, particularly with loft and cavity wall insulation.
Local energy policies and the rising cost of energy are expected to sustain demand, although the scale of new building projects is lower compared to other UK regions.
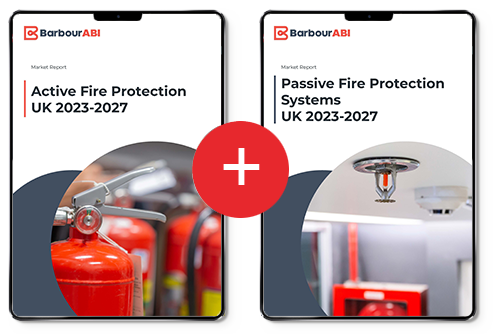
Paired Report Discount
Save £250 for every two reports you buy
Discount applied in basket
Frequently bought together
Trusted by industry leaders
For more detailed requests speak to our research experts directly
By using this form you agree that your data will be processed and protected in line with our Privacy Policy.
Research you can depend on
Our reports go deeper to give you the insights needed to make your next strategic move.
- Detailed assessment of the market – analysis of the market structure and recent developments within the market.
- Market prospects up to 4 years – market value, opportunities, impact of Covid-19, Brexit etc.
- Detailed information – market size, influences, market factors and key players.
- Analysis by product group – market size, product mix, sector trends etc.